The rear suspension in the Bugeye is comprised of the quarter elliptical leaf springs, the shock absorbers, the radius arms and their mounting boxes, the rebound straps, the rubber bump stops, and of course, the axle. Video Episode Thirteen shows the removal of the original fifteen leaf springs: https://vimeo.com/769992972/c923375ecc
We chose to replace the original springs. The only springs readily available at this time are the 10 leaf “Rally” springs. We ordered a pair from BugeyeGuy.com along with five degree shims that will lower the car to give it a proper ride height. We disassembled these springs, removed the poor paint, cleaned them and repainted with POR-15 and installed teflon tape between each leaf to reduce friction and squeaking. That process is shown in Video Episode Fourteen: https://vimeo.com/754389824/9ab8550b67
Most of what we have read on the various forums is that the rally spec springs are a bit stiff and don’t give the ride that the original springs provided. Tom Colby of Speedwell Engineering has suggested the removal of three of the leaves to offer an improved ride and we decided to try his suggestion. We can always back up and reinsert the leaves we take out.
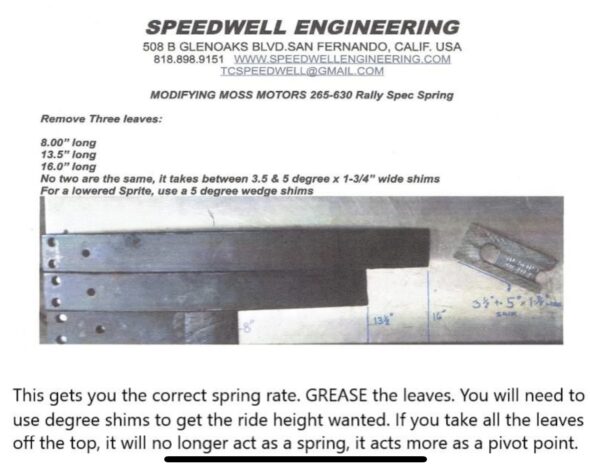
Tom Colby’s Spring Modification
Bugeye Restoration Video Episode Sixty-four shows the deconstruction of the springs.https://vimeo.com/989814778/55abef9a4c
It wasn’t quite as easy as just pulling out a few spring leaves. Because the remaining collection of seven springs isn’t as high as the ten leaves, the bolts and springs clasps need to be modified as well. The two 3/8″ hex head bolts (per spring) that are 3 1/4″ long were replaced with two bolts that are 2 1/2″ long. The 5/16″ compressing pins that are 2 1/2″ long were replaced with 5/16″ socket head screws. Socket head screws were used because the compressing pins have round heads that also serve to locate the spring in the chassis spring plate. Rather than rounding the edges off of a hex head bolt the socket head should work just fine.
Two of the spring clips or brackets are of sufficient size to permit drilling an additional hole in the arms of the bracket to fit the new spring height. There isn’t room on the other two so we will try them as they are or modify at a later date.
The true test will be the ride and that is still months away!